By: Jay Perkins, P.E. Brierley Associates and Dennis Geisser, Atlas Systems of New England
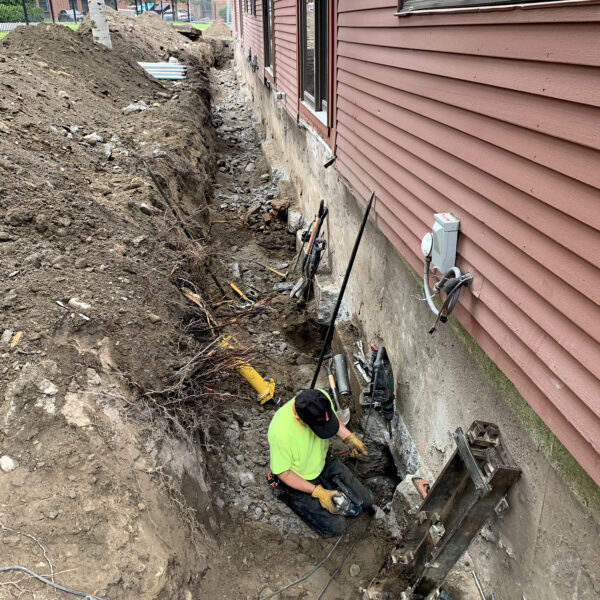
Development of Boston College (BC) Lower Campus began in the 1950’s when the Lawrence Basin of the Chestnut Hill Reservoir was sold to BC and filled in with construction debris. Today BC Alumni Stadium, Flynn Recreation Complex, the Modular Housing Units and training fields and parking areas all occupy this area. Test borings completed for the design of these facilities showed up to 55 feet of fill material and organic deposits overlying very dense Glacial Till and Roxbury Conglomerate bedrock.
The Modular Housing Units, also known as the “Mods” were constructed in the early seventies as temporary housing for students with an intended service life of not more than five years. Fifty years later, these dormitories remain in full use, and have become extremely popular among students and alumni. The 24 residential-type buildings are comprised of rectangular, two-story wood-framed structures supported on a shallow wall footing foundation system bearing directly on the dumped fill material. Over the years, these buildings have undergone significant settlement requiring routine architectural and structural repairs. This settlement is primarily due to the continued long-term consolidation and decomposition of the underlying fill and organic deposits. Other much larger structures built in the same area have not experienced any settlement given their support on a deep pile foundation system extending through the fill material and end bearing on the very dense Glacial Till and bedrock. Although the deep founded structures have not experienced settlement, the surrounding ground surface is expected to do so.
Considering the popularity of the Mods, BC decided these buildings would remain as student housing over the long-term. Engineering consulting firm Kleinfelder of Cambridge was hired by BC to provide an annual settlement monitoring program of the buildings and surrounding area to provide a full understanding of the magnitude of settlement. The program began in 2014 with monitoring the buildings and surrounding ground surface and parking area. Kleinfelder and BC hired Brierley Associates to provide a solution to arrest the on-going settlement of the Mod buildings. Following discussions between Brierley Associates and Atlas Systems of New England, a local Helical and Push Pier installation contractor, it was determined the most economical solution to stop the long-term settlement of the Mod buildings was to underpin the existing shallow foundation system of each building with Earth Contact Products’ (ECP) Push Pier System. These piers are small diameter steel pipe sections hydraulically pushed through the overburden soils to a competent bearing layer thus gaining end bearing support and capacity.
Modular Unit 36-38, located at the north end of the Mod buildings complex was the first building to undergo the improvements. Prior subsurface explorations indicated this unit is on the fringes of the filled reservoir with competent bearing at a depth of 20 feet below existing grade. Designed by Brierley, the Push Pier system for this building consisted of ECP Model 350 Steel Pier 3-1/2 inch O.D. by 0.165 inch wall thickness that is designed for an ultimate and service load of 35.2 kips and 17.6 kips, respectively (FS = 2.0). Based on the building loads, and pier and wall foundation strengths, the maximum pier spacing would be at 6 feet. The pier bracket selected was ECP’s Model 350-400 Utility Bracket with an ultimate capacity of 99 kips. The pier bracket was placed at the bottom/underside of the stem wall following the removal of a 15 inch wide toe section of the exterior side of the footing. For the estimated foundation load and pier spacing at 6 feet on-center, the piers would be installed upon full penetration of the fill materials to the natural soil deposits, proof tested to a jacking pressure of 4,500 psi and locked-off to a final pressure of 2,200 psi.
Initially, the construction schedule was limited to student breaks but faced with the Covid-19 pandemic in March, BC sent all students home which allowed for an early start on pier installation. Atlas Systems immediately applied for the required building permit for pier installation. However, with the pandemic and limited services provided by the City there were concerns with receiving an approved permit in a timely manner. With this work being considered an essential service, the permit was approved in early July. With a July start time, the construction schedule was reduced to approximately 4 weeks and in time for the anticipated return of students to campus in mid-August. This schedule requirement had to be met and no delays could be tolerated to complete the project.
The earthwork contractor, McCourt Construction of Boston, played a significant role with keeping the project on schedule by supporting Atlas Systems during installation of all exterior perimeter piers along the front of the Mod Unit 36-38. Their construction activities included careful excavation by vacuum methods around all existing utilities, removal and disposal of all unsuitable materials, backfill with imported Structural Fill material around the entire perimeter, and asphalt paving to finish grade as needed.
The following provides some pier installation details and obstacles encountered during the underpinning of Mod building 36-38:
- A total of 60 piers were required to underpin the building; 44 along the outside perimeter and 16 along the interior center wall.
- Underpinning the building proved extremely difficult with encountering undocumented utilities and numerous oversized obstructions within the fill material.
- The installation of two test piers were attempted prior to production pier installation. With the exception of encountering No. 9 size reinforcement in the existing footing during bracket installation, the first pier was installed without difficulty. Generally, this would be considered unusually oversized reinforcement for a shallow footing with a 4-foot high stem wall. The test pier was installed to the 20 foot design depth installation pressure of 5,000 psi.
- Undocumented utilities were encountered while excavating to footing depth for the second test pier. Given the buildings were originally considered temporary housing, no as-built utility drawings were generated. Unfortunately, a coaxial cable was encountered, and a high voltage cable was severed resulting in not allowing enough time to complete the installation with the given schedule limitations.
- With the one successful test pier installation, it was decided by BC and Brierley to move forward with underpinning the building.
- As excavation started for production pier installation, again undocumented utilities were encountered that required modification to the pier design locations.
- With unknown utility locations, conventional excavation methods could not be used. Along the front of the building, a Vactor Machine was used by McCourt Construction to carefully remove soil by vacuum methods to footing foundation level. In addition, the pier bracket was changed from a footing mount to a wall-mounted system to minimize the excavation depth and disturbance at the ground surface.
- Once the excavation was complete to footing level and pier installation began, again numerous obstructions were encountered now below footing level. In some cases, these obstructions had to be drilled, lag bolted, chained and pulled out with an excavator. These obstructions consisted of large concrete slabs, brick and ornamental granite. As a result, up to 30 percent of the piers had to be relocated and reinstalled.
- Without the obstructions, the production pier installation rate was up to 6 piers per day. With the presence of obstructions, the production dropped in some cases to 1 to 1-1/2 piers per day.
Because of the delays with the permit approval process, and with the slower rate with production pier installation, only the outer perimeter piers were installed by the August deadline when students returned to campus. The remaining 14 interior piers will be installed during the next student break.
Moving forward with underpinning the remaining buildings, the additional time and cost with encountering obstructions in the fill material for 30 percent of the piers installed proved challenging to the team who is now re-evaluating the Push Pier System at this site.
The presence of obstructions can typically be determined by the degree of difficulty with drilling the test borings and erratic Standard Penetration Test (SPT) blow counts recorded in the borings. However, for this building the ease with drilling the two completed test borings through the fill material, and the relatively consistent recorded SPT blow counts were not indicative of any obstructions. The two test piers also showed minimal obstructions. Given the experience gained during this initial work, underpinning the remaining buildings, that are situated upon thicker zones of fill, will be more challenging. An alternative system considered for underpinning might be a drilled method, such as ECP’s Micro-Pile system. The drilled method could provide for a more efficient installation through the fill and associated obstructions
However, the Push Pier System with obstructions could prove more economical than the drilled method and will ultimately be determined based on the results of additional test borings and test piers completed at the remaining buildings.
Project Team:
Push Pier System Installation Contractor: Atlas Systems of New England
Push Pier System Designer: Brierley Associates
Project Engineer: Kleinfelder
Earthwork Contractor: McCourt Construction